Offsite Construction
The construction industry is changing. Moving to more environmentally friendly bulding methods is essential, while increasing density and removing supply side bottlenecks all require a new approach to traditional construction methods. At Jacks we firmly believe that wood is the material of the future. We also believe shifting construction off the building site into controlled factory environments is not just an opportunity, but an inevitability.
In the residential area, closed or semi-closed timber frame panels form the basis of an extremely rapid building system. Already a reality in NZ, entire walls are shipped to site - not just the frames, but millimetre perfect wall panels up to 12 metres long comprising of insulation, services, gypsum board, cladding, and even joinery. Such a system can achieve a weathertight building envelope in less than a day on a prepared foundation, dry and ready for finishing trades to complete the interior.
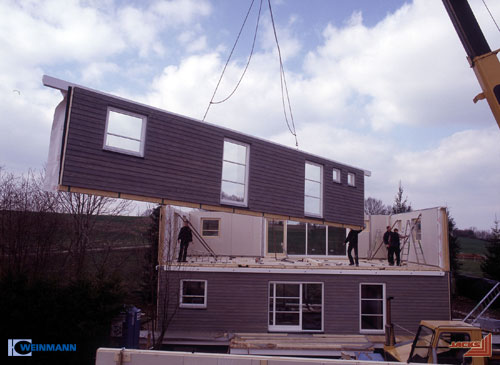
While all buildings can use this system and gain significant improvements in speed and quality compared to site building, markets where panelised timber frame are especially competitive are:
- Low- to mid-rise apartments and townhouses
- Medium to large developments of detached townhouses
- Difficult, steep, or remote sites where access for traditional builds is impossible or expensive.
- 2-4 story residential developments
- Schools, retirement villages, and light commercial developments
- Hybrid building systems comprising of structural engineered wood products and infill timber frame panels.
Jacks primarily supplies panelisation solutions from our partners Weinmann, based in Germany. Production solutions exist from small, mostly manual operations to large, automated turnkey lines capable of over a thousand houses per year.
In the commercial building space, the building material of choice in the 21st century is focusing on wood. Worldwide, recognitions is building that buildings constructed from engineered wood products (EWP) can start life in carbon credit, and offer significant benefits over concrete and steel.
Engineered wood is not a system that relies on its green credentials, however - it is strongly competitive. The largest advantage of engineered wood products is their speed on site - timber is around 20% of the weight of concrete, and faster shipping, handling, and placement of products can slash project timelines, delivering buildings for occupancy in record time.
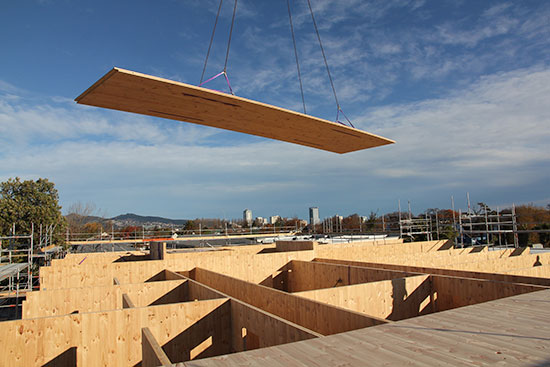
Broadly speaking, EWP are divided into two broad categories - panel products such as cross laminated timber (also known as CLT) and beam products such as Glulam and LVL.
CLT can be used for floor, wall, or roof elements in all types of buildings, but areas where it is known to be an especially competitive solution include:
- Midrise apartments and townhouses from 2-10 storeys
- Floor elements on steep sites or difficult land, enabling you to get out of the ground quickly
- Hotels, hostels, student accommodation, hospitals, and aged care facilities - these buildings often enable a very efficient "honeycomb" structural solution through repeating floor plans
- Midfloors and mezzanine floors for light industrial buildings
- Shear walls in combination with other structural beam systems like Glulam or LVL.
Jacks are proud to have been involved with Red Stag Timber Solutions' CLT plant . View a site tour online
Glulam and LVL are generally used as structural frame products for large buildings in a column and beam configuration. These advanced timber structures are notable for their seismic performance - and their good looks! There are several other applications for these beam products:
- LVL is sometimes used as a substitute for solid lumber in timber framing where stiffness, stability and straightness are especially important.
- Glulam can be pressed into a curved beam - combined with CNC machining capabilities, this can result in incredible unique structures and impressive clearspan spaces.
![]() |
![]() |
![]() |
![]() |
As an independent supplier with extensive experience in the New Zealand market we are able to tailor a solution to your specific production requirements. Let’s talk!